1/ Nguyên công khoan
Nguyễn công khoan được xác định theo kiểu lỗ khoan hoặc kiểu dụng cụ cắt.
Bảng 25.1: Phân loại nguyên công khoan
Kiểu dụng cụ cắt | Kiểu lỗ gia công |
Mũi khoan tâm | Lỗ suốt |
Mũi khoan điểm | Lỗ vát miệng (lả miệng) |
Mũi khoan Xoắn | Lỗ bán cụt |
Mũi khoan khoét | Lỗ cụt |
Mũi khoan chắp | Lỗ khoan sẩn |
Mũi khoan đặc biệt |
1.1/ Các kiểu mũi khoan
Mũi khoan được phân loại theo thiết kế và theo kích cỡ. Thiết kế phổ biến nhất là lâu đời nhất là mũi khoan Xoắn, thường được chế tạo bằng thép gió (tháp dụng cụ cát gọi tốc độ. cao), hợp kim Fe-Co, hợp kim cứng (carbiđes),… Các thiết kế khác bao gồm mũi khoét, khoan tâm, khoan điểm (lả miệng), mũi khoan chắp mảnh carbides. Sự khác biệt về kích cỡ không chỉ giữa các mũi khoan hệ Anh và hệ mét, mà còn được phân loại kỹ hơn với các đơn vị Anh. Do kích thước theo hệ Anh dựa trên đơn vị inch (tương đối lớn), cần có sự phân biệt chi tiết hơn. Kích thước inch của các mũi khoan tiêu chuẩn theo hệ Anh được chia làm ba nhóm:
- Kích cỡ phân số: 1/64 là nhỏ nhất, số gia đường kính (tăng dần) theo 1/64
- Kích cỡ theo số: Số cỡ mũi khoan 80 đến số cỡ mũi khoan 1
- Kích cỡ theo chữ:Chữ kích cỡ mũi khoan từ A đến Z.
Kích cỡ hệ mét không cần các phân loại đặc biệt. Đối với kích cỡ Anh, bạn có thể xem nhiều tài liệu để biết mũi khoan tiêu chuẩn và đương lượng thập phân của chúng.
1.2/ Các xem xét lập trình
Mũi khoan tiêu chuẩn, bất kế kích cỡ, có hai tính năng quan trọng, đường kính và góc đỉnh. Đường kính được chọn theo các yêu cầu của bản vẽ, góc đỉnh liên quan đến độ cứng của vật liệu gia công. Chúng quan hệ chặt chẽ với nhau, đường kính xác định kích cỡ lỗ khoan, góc đỉnh xác định chiều sâu. Điều thứ hai cần xét là số rãnh thoát phoi, mũi khoan tiêu chuẩn có hai rãnh.
1.3/ Đường kinh mũi khoan danh định
Khảo sát Cơ bản là đường kính. Nói chung, đường kính và mũi khoan được chọn dựa vào dữ liệu trên bản vẽ. Nếu bản vẽ cho biết lỗ chỉ khoan và không cần gia công bổ sung, chỉ cần dùng mũi khoan tiêu chuẩn. Đường kính mũi khoan tương đương với kích cỡ lỗ trên bản vẽ. Cỡ mũi khoan này được gọi là đường kính danh định (Hình 25.5).
Hầu hết các ứng dụng đều gồm các lồ đòi hỏi thêm các đặc tính kỹ thuật bổ sung cho đường kính, chẳng hạn dung sai, độ bóng bề mặt, lả miệng, độ đồng tâm … Trong các trường hợp đó, không thể dùng một mũi khoan tiêu chuẩn để đáp ứng tất cả các yêu cầu. Mũi khoan danh định, không bảo đảm lỗ chất lượng cao, do các điều kiện gia công. Sự lựa chọn kỳ thuật nhiều dụng cụ cắt để gia công lỗ này là hoàn toàn hợp lý. ứng dụng chung trong những trường hợp đó là dùng mũi khoan hơi nhỏ hơn đường kính lỗ hoàn tất, sau đó dùngthêm các dụng cụ cắt khác, có khả năng hoàn thiện lỗ theo các yêu cầu bản vẽ. Các dụng này gồm thanh doa, dao chuốt, dụng cụ lả miệng, phay, V…V… Sử dụng các dụng cụ đó sẽ tăng khối lượng công việc nhưng cho phép bảo đảm chất lượng gia công.
Hình 25.5. Đường kính khoan danh định và đường kính hiệu dụng (mũi khoan Xoắn).
2/ Khoan lỗ suốt
Khoan lỗ suốt qua chi tiết là nguyên công rất phổ biến. Khoan lồ suốt yêu cầu chiều sâu Z, gồm chiều dày vật liệu, chiều dài đỉnh mũi khoan và khoảng hở phía sau điểm xuyên thâu của mùi khoan, được gọi là giá trị xuyên qua.
Hình bên dưới minh họa chiều sâu lập trình cho lỗ suốt là tổiig chiều dày vật liệu T, tương đương với chiều sâu đường kính toàn phần F, cộng khoảng hở xuyên qua C, và chiều dài đỉnh P.
Hình 25.8. Dữ liệu tính toán chiều sâu khoan. Lỗ suốt (trên) và lỗ cụt (dưới)
Ví dụ, nếu chiều dày vật liệu là một inch, đường kính mũi khoan 05/8 (0.G25) inch, chiều sâu lập trình, với khoảng hở 0.050 inch sẽ là: 1 + .050 + (5/8 x .300) = 1.2375.
Bạn hãy chú ý các chướng ngại (bàn máy, đồ gá, ngàm kẹp,…) khi lập trình khoảng hở xuyên qua. Nói chung, khoảng trống ở mặt dưới chi tiết thường rất nhỏ.
2.1/ Điều khiển chiều sâu khoan xuyên
Phương pháp lập trình ít được sử dụng, nhưng rất hiệu quả, là sử dụng chu kỳ khoan gián đoạn đến điều khiển sự xuyên qua của mũi khoan lỗ suốt, bất kể kích cỡ mũi khoan hoặc chiều dày vật liệu. Dưới đây là các cơ sở. Trong nhiều vật liệu có độ dẻo cao, khi mũi khoan bắt đầu xuyên đến đáy chi tiết (khoan lỗ suốt), có thể xuât hiện các điều kiện khó gia công. Mũi khoan có xu hướng đẩy vật liệu ra ngoài thay vì cắt gọt. Điều này rất phổ biến khi mũi khoan hơi cùn, vật liệu có độ dẻo cao, hoặc tốc độ cắt hơi cao. Các điều kiện bất lợi này còn làm cho nhiệt phát sinh ở lưỡi cắt, thiếu bôi trơn ở đầu mũi khoan, và các yếu tố khác.
Giải pháp khả dĩ cho vấn đề này là giám áp suất mũi khoan khi mũi khoan ở khoảng nửa dường xuyên qua lỗ, nhưng chưa hoàn toàn xuyên qua (Hình 25.11).
Hình 25.11. Điều khiển sự xuyên qua lỗ sử dụng chu kỳ khoan G83.
Chu kỳ khoan gián đoạn G83 là rất thích hợp, nhưng tính toán chiều sâu Q là cực kỳ quan trọng. Tổng số đoạn không quan trọng, chỉ hai đoạn cuối là có tính quyết định đối với mục đích này. Để kiểm soát vấn đề liên quan đến sự xuyên thấu mũi khoan, chỉ cần hai chuyển động. Hình 25.11 minh họa hai vị trí mũi khoan ø1/2 khoan qua tấm dày 3/4 inch.
Đối với nhiều ứng dụng, loại lỗ này không yêu cầu xử lý đặc biệt chỉ cần một lần cắt xuyên qua (sử dụng chu kỳ G81) và không cần khoan gián đoạn. Bạn hãy đánh giá giải pháp của tình huống này. Mũi khoan ø.5 có chiều dài đỉnh .300 X 500 = .150. Bạn hãy lấy một nửa chiều dài đỉnh mùi khoan (.075) làm giá trị xuyên qua thứ nhất, sẽ đưa mũi khoan xuống dưới tấm dày 3/4 inch một khoảng là .075 inc.h, đến chiều sâu Z-0.825. Chiều sâu này sẽ đạt được với giá trị chiều sâu Q. Bạn cần nhớ chiều sâu Q là giá trị số gia, đo từ mức R, trong trường hợp này là R 0.1. Điều đó sẽ chuyên biệt chiều sâu Q là Q 0.925 (.100 trên và .825 dưới Z0). Chiều sâu Z lập trình là chiều sâu khoan hoàn tất. Nếu cộng thêm khoảng hớ .05 dưới tấm phôi, -chiều sâu Z sẽ là tổng chiều dài phôi (.75), khoảng hở (.05), và chiều dài đỉnh mũi khoan (.150), giá trị lập trình là Z-0.95:
G99 G83 X. . Y. . R0 . 1 Z-0 . 95 QO . 925 F . .
Kỹ thuật này khồng chí giải quyết vấn đề liên quan đến chi tiết cụ thể, mà còn cho thây tính sáng tạo trong lập trình là không thế thiếu.
3/ Khoan lỗ cụt
Khác biệt cơ bản giữa khoan lỗ cụt và lỗ suôt là mũi khoan không xuyên qua vật liệu. Khoan lỗ cụt hầu như tương tự khoan lỗ suốt, riêng đốì với lỗ sâu phải sử dụng phương pháp khoan nhiều đoạn. Ngoài ra, sự lựa chọn dạng hình học thích hợp cho mũi khoan sẽ góp phần cải thiện sự gia công, đồng thời cần làm sạch lỗ khoan.
Trên bản vẽ, chiều sâu lỗ cụt được xác định theo chiều sâu có đường kính toàn phần. Chiều dài đỉnh mũi khoan thường không được coi là một phần của chiều sâu đó, chỉ cộng vào chiều sâu đã chuyên biệt. Trên Hình 25.8, chiều sâu lập trình của lỗ cụt là tổng chiều sâu đường kính toàn phần F và chiều dài mũi khoan P.
Ví dụ, mũi khoan tiêu chuẩn 03/4 (0.750) được dùng để khoan chiều sâu lỗ đường kính toàn phần 1.25 inch, chiều sâu lập trình sẽ là: 1.25 + (.750 x .300) = 1.4750
Trong chương trình gia công, block sẽ là N93 G01 Z-1.475 F6.0 hoặc, nếu dùng chu kỳ cố định N93 G99 G85 X5.75 Y8.125 R0.1 Z-1.475 F6.0
Các lỗ hệ mét cũng được xử lý tương tự. Ví dụ, mũi khoan ø16 mm được dùng để gia công chiều sâu đường kính toàn phần 40 mm. Tính toán sử dụng hệ số (Bảng 25.2) hoàn toàn như với đơn vị Anh: 40 + (16 x 0.300) = 44.8
Chiều sâu (40 mm) ghi trên bản vẽ được cộng thêm chiều dài đỉnh mũi khoan (16 X 0.300). Block lập trình có giá trị trục Z bằng tổng chiều sâu 40 mm và chiều dài đỉnh tính toán 4.8 mm.
N56 G01 Z-44.8 F150.0
Nếu dùng chu kỳ cố định, giá trị trục Z vẫn là 44.8, nhưng có định dạng khác.
N56 G99 G87 X215.0Y175. – R2.5 Z-44.8 F150.0
Khi gia công lỗ cụt, phoi cắt có thể kẹt trong lỗ. Điều này sẽ gây ra vấn đề, đặc biệt khi có nguyên công kế tiếp trong lỗ, chẳng hạn chuốt hoặc tarô ren. Bạn cần đưa mã dừng chương trình M00 hoặc M01 vào trước nguyên công đó. M00 là lựa chọn tốt hơn, nếu cần làm sạch lỗ mỗi khi thực thi chương trình. Nói chung, mã dừng chương trình tuỳ chọn M01 cũng đủ cho phép làm sạch lỗ.
4/ Khoan lỗ đáy phẳng
Lỗ đáy phẳng là lỗ cụt với đáy 90° theo đường tâm khoan. Có hai phương pháp lập trình để gia công kiểu lỗ này. Bạn có thể dùng mũi khoan tiêu chuẩn để khoan lỗ sau đó dùng mũi khoan đáy phẳng có cùng đường kính để hoàn tất lỗ đến chiều sâu toàn phần. Phương pháp thứ hai là dùng dao phay mặt đầu, không cần khoan trước. Đây là phương pháp tốt nhất, nhưng có thể không có một số cỡ dao phay.
Lập trình lỗ đáy phắng với dao phay mặt đầu tương đôi đơn giản. Ví dụ, gia công lỗ 010 mm đáy phẳng, sâu 25 mm. Sử dụng dao phay mặt đầu 010 mm, chương trình sẽ rất ngắn nếu dao đã lắp trong trục chính.
Bạn còn có thể dùng chu kỳ cố định với vài chỉnh sửa để gia công lỗ đáy phẵng.
Ví dụ kế tiếp là chương trình với hai dụng cụ cắt, mũi khoan tiêu chuẩn 01/2 inch và mũi khoan đáy phẳng 01/2 inch. Chiều sâu hoàn tất với đáy phẳng là Z-0.95:
Bạn hãy chú ý ba block trong chương trình O2503. Thứ nhất là block N6, biểu thị chiều sâu mũi khoan tiêu chuẩn. Mũi này dừng lại trước chiều sâu toàn phần khoảng 0.010 inch. Giá trị Z-0.94 được lập trình thay vì Z-0.95. Lý do không khoan đến chiều sâu toàn phần với mũi khoan tiêu chuẩn là để tránh gây ra vết đỉnh dao ở tâm lỗ.
Hai block tiếp theo trong phần dao thứ hai của chương trình – block N14 và block N15. Trong N14, mũi khoan đáy phẳng gia công với tốc độ cắt lớn chỉ đến chiều sâu 0.740 inch, do mũi khoan đáy phẳng hầu như không cắt gọt cho đến chiều sâu đó. Bạn hãy xem sự tính toán chiều sâu trung gian 0.740 từ quy trình dưới đây:
Từ chiều sâu toàn phần 0.94 được cắt gọt bằng mũi khoan tiêu chuẩn (TOI), bạn hãy trừ chiều dài đỉnh dao p. Đó là 0.15 với góc đĩnh 118° của mũi khoan ø.5. Kết quả là .79. Từ kết quả đó, bạn trừ khoảng hở 0.50 để có giá trị trục Z là Z-.74. Trong block N15, mũi khoan đáy phẳng sẽ cắt lượng còn lại từ TOI, với tốc độ cắt thích hợp, thường được lập trình với tốc độ đủ chậm.
Theo quan điểm gia công, lập trình mũi khoan tâm hoặc khoan điểm trước để khởi đầu lồ gia công sẽ thuận tiện hơn. Nguyên công này sẽ bảo đảm độ đồng tâm cho cả mũi khoan tiêu chuẩn và mũi khoan đáy phẳng. Sự cải thiện tiếp theo là dùng dao phay mặt đầu thay cho mũi khoan đáy phẳng. Dao này thường có độ cứng vững cao hơn và độ chính xác lớn hơn.
Khoan bằng mũi khoan gắn mảnh hợp kim
Một trong các dụng cụ cắt năng suất cao trong gia công hiện đại là mũi khoan gắn mảnh hợp kim (còn gọi là mũi khoan chắp).
Loại mũi khoan này sử dụng các mảnh carbides (hợp kim cứng) tương tự các dao phay hoặc tiện. Mũi khoan được thiết kế để khoan vật liệu rắn, không yêu cầu khoan tâm hoặc khoan điểm, tốc độ trục chính cao và tốc độ cắt tương đối thấp. Trong hầu hết các trường hợp, loại mũi khoan này được dùng để khoan các lồ suốt, nhưng cũng có thể khoan lỗ cụt. Kiểu mũi khoan này còn được dùng để doa với lượng dư gia công thấp đến trung bình.
Thiết kế của mũi khoan chắp rất chính xác, bảo đảm chiều dài dụng cụ cắt không đổi, hầu như không cần mài lại lười cắt bị mòn. Hình 25.9 minh họa phần cắt gọt của mũi khoan chắp thông dụng.
Trong minh họa này, đường kính D của mũi khoan là kích cỡ lỗ do mũi khoan tạo ra. Chiều dài đỉnh H do nhà chế tạo mũi khoan xác định. Ví dụ, mũi khoan chắp với đường kính D = 1.25 inch, có chiều dài đỉnh H là .055. Mũi khoan này có thể dùng cho ứng dụng quay hoặc tĩnh tại, ngang hoặc đứng, trên trung tâm gia công hoặc máy tiện. Để đạt hiệu suất cao, cần cung cấp chất làm nguội với áp suất cao qua suốt chiều dài mũi khoan đặc biệt khi gia công các vật liệu cứng, lỗ sâu, hoặc nằm ngang. Chất làm nguội không chỉ giải nhiệt mà còn giúp đẩy phoi ra ngoài. Khi sử dụng mũi khoan chắp, cần bảo đảm đủ công suất ở trục chính của máy. Các yêu cầu công suất tại trục chính tăng tỷ lệ với đường kính mũi khoan.
Trên trung tâm gia công, mũi khoan chắp được lắp vào trục máy, do đó quay chung với trục. Theo kiểu lắp này, mũi khoan được dùng trong trục chính phải có độ cứng vừng cao. Sự cung cấp chất làm nguội có thể gộp cả chất làm nguội bên trong, bộ ống thích hợp để làm nguội qua lỗ khi mũi khoan được dùng trên trung tâm gia công.
Trên máy tiện, mũi khoan chắp luôn luôn tĩnh tại. Giá lắp chính xác đòi hỏi mũi‘khoan định vị ở tâm và đồng tâm với đường tâm trục chính.
Cần rất cẩn thận khi khoan trên bề mặtkhông phẳng. Đế’ có kết quả tốt, bạn hãy dùng mũi khoan chắp trên C&C bề mặt vuông góc (90°)với trục mũi khoan (bề mặt phẳng). Trong các giới hạn đó, mũi khoan còn có thể được dùng để vào hoặc ra bề mặt nghiêng lồi, hoặc lõm. Cần giám tốc độ cắt trong khi cắt gián đoạn. Hình 25.10 minh họa các vị trí cần giám tốc độ.
Hình 25.10. Bề mặt vào hoặc ra không đều đối với tốc độ cắt của mũi khoan chắp: F = tốc độ cắt bình thường, F/2 = giám tốc độ cắt (một nửa F).
Trong minh họa này, chữ F biểu thị vùng được cắt với tốc độ cắt bình thường (vào/ra bình thường), F/2 biểu thị vùng yêu cầu giám tốc độ cắt. Đối với sự giám tốc độ cắt, chỉ cần lập trình một nửa tốc độ cắt bình thường là đủ.
Trên Hình 25.10, hình a là bề mặt nghiêng, b là bề mặt không đều, c và d là các bề mặt lồi và lõm.
Mũi khoan chắp chủ. yếu dùng cho khu vực gia công được bảo vệ
5/ Khoan nhiều đoạn trong một lỗ
Phương pháp này còn được gọi là khoan cắt gián đoạn. Đây là nguyên công khoan, sử dụng các chu kỳ cố định G83 (tiêu chuẩn) hoặc G73 (tốc độ cao). Khác biệt giữa hai chu kỳ này là phương pháp lùi dao. Trong G83, sự lùi dao sau mỗi đoạn đến mức R (phía trên lỗ), trong G73, chỉ lùi dao rất ngắn (khoảng 02 – .04 inch).
Khoan nhiều đoạn thường dùng cho các lỗ quá sâu đối với một chuyển động dao. Các phương pháp khoan nhiều đoạn còn có vài cơ hội cải tiến kỹ thuật khoan tiêu chuẩn. Dưới đây là một số ứng dụng của phương pháp này khi gia công các lỗ:
- Khoan lỗ sâu.
- Bẻ gãy phoi – có thể dùng cho cả các lỗ ngắn trong vật liệu dẻo.
- Làm sạch phoi tích tụ trong các rãnh thoát phoi của mũi khoan.
- Làm nguội và bôi trơn thường xuyên cho các lưỡi cắt củamũi khoan.
- Kiểm soát mũi khoan khi xuyên vào vật liệu.
Trong tất cả các trường hợp, các chuyển động khoan của chu kỳ G83 hoặc G73 tạo ra sự cắt gián đoạn có thể được lập trình rất đơn giản bằng cách chuyên biệt giá trị địa chỉ Q trong chu kỳ. Giá trị này là chiều sâu thực của từng đoạn khoan. Giá trị Q càng nhỏ, số đoạn khoan càng lớn và ngược lại. Đối với hầu hết các nguyên công khoan sâu, số lượng chính xác các đoạn khoan không quan trọng, nhưng có những trường hợp cần điều khiển chu kỳ khoan nhiều đoạn.
5.1/ Ứng dụng khoan nhiều đoạn
Đôi với hầu hết các ứng dụng khoan nhiều đoạn, chiều sâu Q chỉ cần là chiều sâu hợp lý. Ví dụ, lỗ sâu (với chiều sâu Z-2.125 inch ở đỉnh dụng cụ) được khoan với mũi khoan đường kính .250 và chiều sâu từng đoạn là .600. Chu kỳ G83 có thể lập trình như sau:
N137 G99 G83 X. . Y. . R0.1 – Z-2.125 Q0.6 F8.0
Các giá trị lập trình này là hợp lý. Đối với hầu hết các ứng dụng, số lượng các đoạn khoan thường không quá quan trọng.
5.2/ Tính toán số đoạn khoan
Nếu số đoạn khoan trong chu kỳ G83/G73 là quan trọng, cần phải tính toán giá trị đó. Biết số đoạn và giá trị Q đối với chiều sâu toàn phần cho trước thường không quan trọng. Nếu chương trình chạy hiệu quả, thì không cần chỉnh sửa. Để tìm số’ đoạn thích hợp cho chu kỳ G83/G73, điều quan trọng là biết khoảng cách toàn phần của hành trình mùi khoan giữa mức R và chiều sâu Z (theo giá trị số gia). Điều quan trọng tiếp theo là biết giá trị Q. Khoảng cách hành trình chia cho Q sẽ được số đoạn cần khoan:
Trong đó:
- Pn = số đoạn
- Td = Khoảng cách toàn phần hành trình dao
- Q = Chiều sâu đoạn được lập trình
Ví dụ, trong chu kỳ G83 NT3 G99 G83 X Y R0.125 Z-1.225 Q.05 P12.0
Khoảng cách hành trình toàn phần là 1.350 chia cho .500 sẽ được kết quả là 2.7. Do số đoạn chỉ có thể là số nguyên, số nguyên lớn hơn gần nhất sẽ là số đoạn, trong trường hợp này là số 3.
5.3/ Chọn số đoạn
Trong thực tế thường lập trình với số đoạn Mong muốn. Nếu chỉ một số lượng xác định các đoạn là đủ để đạt hiệu suất tốì ưu, từ đó có thể dễ dàng tính giá trị Q. Do giá trị Q chuyên biệt chiều sâu của từng đoạn khoan nhưng không xác định số đoạn, cần dùng công thức toán để chọn chiều sâu Q, tương ứng số đoạn Mong muốn.
Ví dụ, bạn cần ba đoạn khoan trong chu kỳ dưới đây, giá trị chiều sâu Q sẽ là:
N14G99GR3X.. Y. . R0 . 1 Z-1.238 Q . . F12.0
Hành trình khoan toàn phần từ mức R đến chiều sâu Z là 1.338 inch. Để tính giá trị Q, công thức có dạng:
Trong đó:
- Q = Chiều sầu đoạn được lập trình
- Td = Khoảng cách toàn phản hành trình dao.
- Pn = Số đoạn mong muốn.
Sử dụng công thức nêu trên, kết quả 1.338/3 là .446. Do đó, chiều sâu Q trong block G83 là Q0.446:
N14 G99 G83 X. . Y. . R0.1 Z-1.239 Q. . F12.0
Trong trường hợp này không cần làm tròn số. Bạn hãy quan sát tình huống khác, khoảng cách hành trình thay đổi rất ít:
N24 G99 G83 X. . Y. . R0.1 Z-1.239 Q. . E12.0
Kết quả của 1.339/3 là .446333333 – sô cần được làm tròn đến 4 chữa số thập phân (đơn vị Anh). Về toán học, làm tròn với 4 chữ số thập phân là .4463. Bạn hãy quan sát chiều sâu của từng đoạn.
Đoạn 1 .4463 Chiều sâu tích lũy … .4463
Đoạn 2 .4463 Chiều sâu tích lũy … .8926
Đoạn 3 .4463 Chiều sâu tích lũy … 1.3389
Đoạn 4 .0001 Chiều sâu tích lũy … 1.3390
Ớ đây cần đến bốn đoạn và đoạn cuối chỉ cắt .0001, hầu như không đáng kể. Trong các trường hợp đó, với lần cắt cuối cùng rất nhỏ và không hiệu quả, bạn cần làm tròn giá trị Q theo hướng tăng, trong ví dụ nêu trên, tối thiểu là .4464, có thể làm tròn đến .447.
N14 G99 G83 X Y R0.1 Z-1.239 Q0.447 F12.0
Bạn cần nhớ, dụng cụ cắt không bao giờ vượt quá chiều sâu Z lập trình nhưng có thế đến chiều sâu này với cách thức rất không hiệu quả, do đó cần hiệu chỉnh.
6/ Khoan nhiều bậc
Khoan qua nhiều bậc là nguyên công khoan giữa hai hoặc nhiều chi tiết, cách nhau bằng khoảng không gian trống’. Vấn đề lập trình là gia công các lỗ này một cách hiệu quả. Có thể dễ dàng lập trình một chuyển động xuyên qua tất cả các chi tiết riêng rẽ và các khoảng trống. Đối với nhiều lỗ, phương pháp này có lẽ không hiệu quả. Bạn hãy khảo sát bản vẽ trên Hình 25.22.
Trong chương trình này, X1.0 Y1.5 là vị trí lỗ. Bản vẽ không nêu rõ mức R và chiều sâu Z, chúng cần được tính toán. Trong ví dự này, khoảng hở trên và dưới từng tấm chi tiết là.05, ngoại trừ mức R thứ nhất (R0.l). Chiều dài đỉnh mũi khoan ø1/4 là 0.3 X 0.25 = 0.075 inch.
Bạn hãy lưu ý, một lỗ yêu cầu đến ba block chương trình, thay vì một block. Mồi block biểu
thị cho một tấm trong chi tiết gia công. Ngoài ra, bạn hãy để ý G98 trong block N16. Chí một lồ được thực hiện trong ví dụ này, do đó G98 là không cần thiết. Lệnh xóa chu kỳ G80 với chuyển động trở về trong block NI7 sẽ lùi dao ra khỏi lỗ. Tuy nhiên, nếu gia công nhiều lỗ, cần dịch chuyển dao đến vị trí XY mới trước khi lập trình G80. Trong trường hợp này, cần có G98 khi mũi khoan xuyên qua tấm cuối cùng của chi tiết. Ví dụ này chưa phải là giải pháp tối ưu đốì với quy trình khoan qua nhiều bậc, do vẫn có chuyển động vô ích. Phương pháp lập trình hiệu quả là sử dụng kỹ thuật lập trình macro.
7/ Khoan tâm
Khoan tâm là nguyên công tạo lỗ nhỏ đồng tâm cho chuôi nhọn ụ động hoặc dẫn hướng để khoan lỗ lớn. Không nên dùng mũi khoan tâm để lả miệng (vạt góc miệng) do góc đỉnh chỉ là 60°.
Không đựợckhoan tâm lỗ sểkhoan với mũi khoan.gắn mảnh hợp kim!
Dụng cụ phổ biến nhất để khoan tâm là mũi khoan tâm tiêu chuẩn (thường được gọi là mũi khoan kết hợp và khoét miệng), tạo ra góc 60°. Tiêu chuẩn công nghiệp Bắc Mỹ sử dụng hệ thống đánh số từ #00 đến #8 và #11 đến #18 cho các mũi khoan tâm. Trong hệ mét, được xác định theo đường kính dẫn hướng, ví dụ mũikhoan tâm 4 mm sẽ có đường kính dẫn hướng 4 mm. Trong cả hai trường hợp, số càng lớn, đường kính mũi khoan càng lớn. Đốì với một số nguyên công khoan sơ bộ, chẳng hạn lả miệng, dụng cụ cắt với góc đỉnh 90°, được gọi là mũi khoan điểm, là loại được dùng phổ biến.
Nhiều nhà lập trình chỉ ước tính chiều sâu khoan tâm, thay vì tính toán.Có lẽ tính toán là không cần thiết cho sự gia công tạm thời. Bạn có thể dùng dừ liệu trên Hình 25.7 để xác dịnh chiều sâu khoan tâm với các mũi khoan có đường kính D khác nhau.
Hình 25.7. Chiều sâu cắt L với mũi khoan tâm tiêu chuẩn.
Hình 25.7 nêu rõ mọi kích thước cần thiết của các mũi khoan tâm tiêu chuẩn theo hệ Anh, trong đó quan trọng nhât là chiều sâu cắt L. Tính toán L dựa trên sự lựa chọn tùy ý đường kính lả miệng D.
Ví dụ, mũi khoan tâm #5 có giá trị chiều sâu L là 0,382, dựa trên đường kính lả miệng được chọn tuỳ ý D = 0.350 inch. Các giá trị này có thể chỉnh sửa theo yêu cầu gia công cụ thể, theo đơn vị hệ Anh hoặc hệ mét.
8/ Chiều dài đỉnh mũi khoan
Vấn đề quan trọng thứ hai là chiều dài của đỉnh mũi khoan. Chiều dài này rất quan trọng để thiết lập chiều sâu dao đến đường kính toàn phần. Với ngoại lệ là mũi khoan đáy phẳng, mọi mũi khoan Xoắn đều có đỉnh côn, cần biết cả góc đỉnh và chiều dài trong lập trình. Các góc này thường theo tiêu chuẩn và cần tính chiều dài thay vì phỏng đoán, do tầm quan trọng của chúng đối với chiều sâu lỗ chính xác (Hình 25.6).
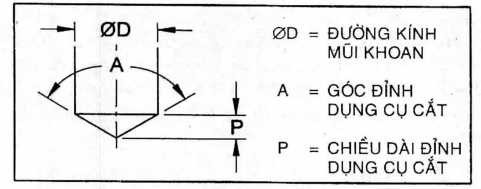
Trên các mũi khoan gắn mảnh hợp kim cứng, chiều dài này hơi khác, do cấu trúc mũi khoan. Loại mũi khoan này không có đáy phẳng do đó cần xét chiều dài đỉnh khi lập trình.
Có thể dễ dàng xác định chiều dài đỉnh mũi khoan nếu biết đường kính (danh định hoặc hiệu dụng) và góc đỉnh. Từ công thức dưới đây và bảng các hệ số (Bảng 25.2), có thể tính chiều dài đỉnh yêu cầu đối với mũi khoan tiêu chuẩn:
Trong đó:
- P = Chiều dài đỉnh
- A = Góc đỉnh
- D = Đường kính mũi khoan.
Công thức này được đơn giản hóa, sử dụng hệ số phân (không đổi đối với từng góc đỉnh)
Trong đó:
- P =Chiều dàiđỉnh
- D = Đường kính mũi khoan.
- K = Hệ số nhân
Bảng 25.2. Hệ số xác định chiều dài đỉnh mũi khoan
Góc đỉnh mũi khoan (Độ) | Hệ số chính xác | Hệ số thực tiễn (K) |
60 | .866025404 | .866 |
82 | .575184204 | .575 |
90 | .500000000 | .500 |
118 | .300430310 | .300 |
120 | .288675135 | .289 |
125 | .260283525 | .260 |
130 | .233153829 | .230 |
135 | .207106781 | .207 |
140 | .181985117 | .180 |
145 | .157649394 | .158 |
150 | .133974596 | .134 |
Hệ số trong công thức được làm tròn với giá trị đủ cho mọi ứng dụng lập trình. Giá trị K đối với góc đỉnh mũi khoan 118° là 0.300, giá trị thực là 0.300430310. Giá trị làm tròn có ưu điểm là dễ nhớ và dễ sử dụng. Đối với hầu hết các ứng dụng, có lẽ chỉ cần 3 hệ số, góc 90° (khoan điểm, khoan vật liệu mềm), 118° (vật liệu tiêu chuẩn) và 135° (vật liệu cứng). Chúng rất dễ nhớ:
- 0.500 góc đỉnh mũi khoan 90°
- 0.300 góc đỉnh mũi khoan 118° – 120°
- 0.200 góc đĩnh mũi khoan 135°