6.6 Hàn vảy
Qua hàn vảy, kim loại có thể kết nối với nhau bằng vật liệu không tháo rời được.
Vật liệu nền và chất phụ gia dễ nóng chảy, gọi chung là chất hàn vảy, được nung nóng đến nhiệt độ làm việc của vảy hàn. ở đây, vật liệu cùa các bộ phận được kết nối vẫn còn ở trạng thái rắn và vảy hàn trở thành lỏng. Khi nguội vảy hàn đông đặc và kết nối các bộ phận lại với nhau. Phạm vi ứng dụng của hàn vảy trải dài từ sửa chữa thủ công đến sản xuất hàng loạt.
Hàn vảy có những ưu điểm sau:
Hàn vảy có những ưu điểm sau:
■ Qua hàn vảy, các kim loại khác nhau cũng có thể được kết nối với nhau dễ dàng.
■ Do nhiệt độ làm việc thấp dẫn đến lợi thế rất lớn khi kết nối các chi tiết với thành dày nhỏ hoặc có độ dày khác nhau. Ngoài ra, giảm nguy cơ phá hủy các chi tiết bởi sự thay đổi cấu trúc, ứng suất nhiệt và hư hỏng (Hình 1 và Hình 2).
■ Phần lớn mối hàn vảy kín đối với hơi và chất lỏng.
Thí dụ về các ứng dụng: Bồn chứa, lắp đặt ống (Hình 2).
■ Mối hàn vảy thông thường dẫn điện tốt.
Thí dụ về các ứng dụng: chế tạo động cơ điện, hàn vảy các kết nối điện và bản mạch in (tấm lắp ráp các bộ phận điện tử).
■ Phương pháp hàn vảy thường được tự động hóa dễ dàng (Hình 3).
Quá trình hàn vảy
Một kết nối hàn vảy được hình thành qua ba giai đoạn (Hình 4). Chất liệu hàn vảy lỏng được phủ lên trên vật liệu nền sạch bằng kim loại và đã được nung nóng đến nhiệt độ gia công, do đó diễn ra sự thấm ướt. Hiện tượng này tạo ra sự tiếp xúc bên trong giữa vật liệu phụ gia và vật liệu nền đồng thời làm chảy vảy hàn. Những giọt vảy hàn lỏng lan ra mở rộng bề mặt tiếp xúc và chảy vào các khe nhỏ nhất. Đồng thời xuất hiện sự cấu tạo hợp kim giữa vật liệu nền và vảy hàn.Để có thể tạo ra sự thấm ướt dựa vào lực bám (lực dính), phải để vảy hàn lỏng tiếp xúc trực tiếp với vật liệu nền. Chỉ cần phủ một ít kim loại rắn với các tạp chất hoặc bao vảy hàn lỏng với oxit, đã ngăn chặn sự tiếp xúc trực tiếp và làm cho kết nối hàn vảy không thể thực hiện được.
Ngay cả sau khi xử lý trước bằng cơ học hay hóa học để hàn, lớp oxit vẫn được tạo thành ngay lập tức ở nhiệt độ phòng.
Phải giảm bớt các lớp phủ oxit kim loại không thấy được bằng cách nung nóng chi tiết và chất vảy hàn trong khí bảo vệ hoặc hòa tan bằng dung môi thích hợp (chất trợ dung).
Dòng chảy và nhờ thế cả sự thấm ướt xảy ra khi khe hở hàn đủ hẹp ở vị trí ngang cũng như thẳng đứng. Hiện tượng này là do tác động mao dân. Tác động mao dẫn dựa vào lực bám giữa chất lỏng và bề mặt rắn (vách khe). Trong vách khe, lực bám chất lỏng tăng lên. Trong ống hẹp lực bám đủ mạnh để hút chất lỏng còn lại lên trên (Hình 1).Bề rộng khe hở hẹp từ 0,05 mm đến 0,2 mm thích hợp nhất cho hàn vảy. ở đây áp suất mao dẫn và nhờ đó chiều cao dâng lên của chất vảy hàn lớn đủ để tự điền đầy vào các khe (Hình 2).
Trong thực tiễn ở xưởng, khe hàn vảy tối ưu đạt được là do bề mặt nhám (gồ ghề) của chi tiết kết nối phần lớn đều bằng các đế thông thường hay các vai chặn. Khe hàn vảy không nên mở rộng theo chiều chảy của vảy hàn, bởi vì qua đó dòng chảy tiếp tục bị cản trở.
Trong phạm vi bề rộng từ 0,2 mm đến 0,5 mm, áp suất mao dẫn để điền đầy giảm đi nhiều. Sự lan rộng vảy hàn và sự điền đầy các khe có thể tình cờ bị cản trở (Hình 3).
Bề rộng mối hàn vảy lớn hơn 0,5 mm ta gọi là khe hở hàn vảy. Hàn vảy cho khe hở thường đòi hói kỹ thuật hán vảy đặc biệt vì áp suất mao dẫn nhỏ.
Giai đoạn hình thành hợp kim xảy ra ngay khi vảy hàn thấm ướt bề mặt. Các nguyên tử của vảy hàn lỏng thâm nhập (di chuyển) vào trong lớp ngoài của vật liệu nền rắn. Tương tự nguyên tử khuếch tán từ vật liệu nền vào trong vảy hàn (Hình 4). Quá trình này được gọi là khuếch tán. Độ sâu của sự thâm nhập phụ thuộc vào vật liệu và nhiệt độ. Vì độ bền của lớp hợp kim cao hơn so với vảy hàn, nên những kết nối hợp kim có độ dày vảy hàn mỏng chịu tải nhiều hơn. Do đó người ta cũng tìm cách làm cho bề rộng khe hở hẹp hơn.
Nhiệt độ hàn vảy
Hàn vảy xảỵ ra trong một phạm vi nhiệt độ nhất định. Giới hạn thấp nhất của nó là “nhiệt độ làm việc”, giới hạn trên là “nhiệt độ hàn tối đa”. Nhiệt độ làm việc là nhiệt độ bề mặt thấp nhất của chi tiết, ờ đó vảy hàn thấm ướt, chảy và hợp kim hóa. Nó được xem như hằng số hàn vảy khi sử dụng chất trợ dung thích hợp.
Khi vượt qua nhiệt độ hàn vảy tối đa không thể có hàn vảy hoàn hảo. Để quá trình hợp kim hóa thuận lợi, sau khi hàn vảy nên giữ nhiệt độ làm việc tùy theo chất liệu hàn 15-60 giây. Lúc nguội và hóa rắn (đông cứng) vảy hàn phải giữ mối hàn không có dao động.
Phương pháp hàn vảy
Khoảng nhiệt độ làm việc giới hạn hai phương pháp hàn vảy mềm và hàn vảy cứng với nhau.
ở hàn vảy mềm, mối hàn mềm và không phù hợp cho việc truyền lực lớn. Điều này là do nhiệt độ làm việc thấp, mà ở đó chỉ có thể hình thành một lớp hợp kim mỏng. Ngoài ra, độ bền của chì, chất hàn vảy được sử dụng chủ yếu, thấp. Nhiệt độ làm việc thấp khiến đường hàn rất nhạy với nhiệt. Do đó phương pháp hàn vảy mềm hiếm khi kết nối được vật liệu sắt. Mặt khác, đồng, thiếc, kẽm và hợp kim của chúng được sử dụng thường xuyên cho việc kết nối và làm kín. Những linh kiện điện tử được hàn với phương pháp hàn vảy mềm.
Hàn vảy cứng thích hợp cho kết nối thép hợp kim và carbon, kim loại cứng, kim loại quý, gang xám, gang dẻo và đồng. Vị trí mối hàn chắc và uốn được. Nó có thể chịu tải cao với điều kiện là thực hiện đúng quy cách. Trong kim loại phi sắt, độ bền của đường hàn thường lớn hơn so với vật liệu nền.
Vảy hàn
Áp dụng cho tất cả vảy hàn:
■ Điểm nóng chảy vảy hàn luôn luôn thấp hơn điểm nóng chảy của vật liệu nền.
■ Là chất đặc biệt rất loãng khi nóng chảy.
■ Kết hợp tốt với các vật liệu kim loại khác.
Các vảy hàn được phân loại theo nhiệt độ làm việc của nó thành hàn vảy mềm và hàn vảy cứng.
Việc lựa chọn vảy hàn được thực hiện bằng cách sử dụng các bảng tra cứu tiêu chuẩn. Từ bảng tra cứu người ta lấy ra các thành phần, phạm vi nóng chảy, nhiệt độ làm việc và hướng dẫn cách ứng dụng.
Việc hàn vảy cho kim loại nhẹ là một vấn đề, vì khó tẩy sạch mặt ngoài bị oxy hóa. Do đó, trong nhiều trường hợp dán hoặc hàn được sử dụng một cách dễ dàng hơn.
Việc hàn vảy cho kim loại nhẹ là một vấn đề, vì khó tẩy sạch mặt ngoài bị oxy hỏa. Do đó, trong nhiều trường hợp dán hoặc hàn được sử dụng một cách dễ dàng hơn.
Theo DIN EN ISO 3677 ký hiệu ngắn cho vảy hàn cứng được trình bày với một chữ B đứng trước. Trong phần thứ hai của ký hiệu ngắn, những thành phần hợp kim được diễn tả bằng ký hiệu hóa học với tỷ lệ phần trăm. Tuy nhiên ở hàn vảy cứng chỉ có tỷ lệ phần trăm của thành phần chính được đưa ra, do đó phần thứ ba được thêm vào chứa thông tin về phạm vi nhiệt độ nóng chảy bằng °c. ở hàn vảy mềm cho linh kiện điện tử là một chữ “E” sau phần thứ hai (xem cẩm nang tra cứu).
Vảy hàn mềm cho kim loại nặng chủ yếu là hợp kim thiếc (Sn) và chì (Pb), để tăng độ cứng và bền người ta thường thêm vào antimon (Sb), bạc (Ag), đồng (Cu) và kẽm (Zn).
Vảy hàn cứng cho kim loại nặng chủ yếu là hợp kim đồng và kẽm hoặc vảy hàn bạc (hợp kim đồng-bạc). Một số chất bổ sung khác có thể là cadimi (Cd), photpho (P), silic (Si), mangan (Mn), thiếc (Sn) và kền (Ni). Kim loại quý bạc (thành phần có khi lên đến 85%) giảm nhiệt độ làm việc xuống 610 °c đến 800 °c (xem cẩm nang tra cứu).
Chất trợ dung hàn
Chất trợ dung hàn là vật liệu phi kim loại. Khi bề mặt vật liệu được làm sạch trước một cách đầy đủ bằng phương pháp cơ học, chất trợ dung và khí bảo vệ có thể loại bỏ các lớp oxit. Như vậy, để vảy hàn có thể thấm ướt bề mặt vật liệu, chất dung môi phải bị đẩy ra ngoài qua hàn (Hình 1). Để tránh sự ăn mòn, phải loại bỏ chất trợ dung hàn còn thừa sau khi hàn vảy xong.
Chất trợ dung để hàn vảy mềm được ký hiệu theo tiêu chuẩn DIN EN 29454 với:
Con số cho kiểu chất trợ dung hàn, chất trợ dung nền và chất trợ dung kích hoạt.
Chữ A được dùng cho chất lỏng, B cho chất rắn và c cho dạng sệt.
Nước hàn vảy (clorít kẽm) có tác động phân hủy thích hợp cho bề mặt bị oxy hóa mạnh với tên gọi 3.2.2.A (F-SW 11).
Bột nhão 2.2.1.C (F-SW 21) ăn mòn nhẹ thích hợp cho hàn vảy đồng.
Chất trợ dung để hàn vảy cứng thường là các hợp chất bor và cũng ăn mòn. Chúng có sẵn cho các phạm vi nhiệt độ tác dụng khác nhau (thí dụ như F-SH2 từ 700 °c -1100 °C).
Kỹ thuật gia còng trong hàn Vày
Trong lúc hàn phải tuân theo các bước gia công nhất định độc lập với phương pháp hàn và trường hợp ứng dụng:
■ Các bề mặt được kết nối phải được làm sạch những lớp oxit, bụi và dầu mỡ bằng phương pháp cơ hoặc hóa học. Điều này thường được thực hiện bằng cách chà xát với giấy nhám hoặc tương tự như vậy, hoặc với các acid thích hợp trong trường hợp hiếm.
■ Chất trợ dung hàn được bôi (trét). Điều này tất nhiên không cần thiết khi chất trợ dung hàn ở dạng sệt (dẻo, nhão) hoặc bột đã được gia công trong chất hàn vảy như trong hầu hết các trường hợp hàn vảy điện.
■ Các vị trí hàn vảy được nung nóng đều với dụng cụ thích hợp.
■ Vảy hàn được đưa vào kết nối với vị trí hàn và được làm nóng chảy.
■ Chỗ hàn nếu càn thiết được làm sạch bằng cách loại bỏ chát trợ dung hàn còn thừa.
Nung nóng vị trí hàn
Đối với hàn vảy mềm thủ công trong lĩnh vực cơ khí, thí dụ như để chế tạo đường ống, người ta thường sử dụng ngọn lửa trong đó bao gồm một hỗn hợp không khí – khí đốt. Ngược lại, trong lĩnh vực kỹ thuật điện và điện tử thường sử dụng trạm hàn, các trạm này dùng mỏ hàn được nung nóng bằng điện như là môi trường truyền nhiệt (Hình 2). Ưu điểm của phương pháp này là nhiệt có thể được hoàn toàn đưa vào một cách có chủ đích, thí dụ như khi gắn linh kiện cho tấm mạch in theo yêu cầu.
Để hàn vảy mềm bằng máy hàn, các bộ phận được nung nóng trong trạm nung nóng trước và sau đó kéo qua một bụng sóng từ vảy hàn thiếc (Hình 3).
Để nung nóng các vị trí hàn vảy nóng, mà trong phạm vi cơ điện tử ít được ứng dụng, hầu như chỉ hàn vảy bằng ngọn lửa từ mỏ hàn hơi hoặc mỏ hàn vảy cứng được sử dụng (Hình 1).
6.7 Hàn
Qua hàn, vật liệu có thể kết nối với nhau bằng vật liệu không tháo ra được.
Các vật liệu được nung nóng tại mối nối (vị trí kết nối) cho tới nhão hoặc lỏng và có thể tự liên kết. Sau khi hóa rắn (đông cứng) phần nóng chảy các chi tiết kết nối với nhau qua cấu trúc chung.
Để đáp ứng yêu cầu đa dạng, hơn 100 phương pháp hàn khác nhau được phát triển. Tùy thuộc vào trình tự củaquá trình hàn ta phân biệt phương pháp hàn ép và hàn nóng chảy (Hình 4).
Phương pháp hàn ép
Qua phương pháp hàn ép vật liệu nền tại những điểm kết nối được nung nóng đến trạng thái nhão và ép lại với nhau. Các chi tiết không cần phải làm nóng chảy ở bề mặt tiếp xúc nên không cần chất phụ gia.
Ở phương pháp hàn ép, sự kết hợp của vật liệu được thực hiện do tác động của nhiệt và sức ép.
Ở hàn điểm (Hình 1) các tấm mỏng hoặc dây nằm chồng lên nhau được kết nối với từng điểm hàn. Hai điện cực đồng nằm đối diện ép các chi tiết lại với nhau và truyền điện, ở các điểm tiếp xúc, các chi tiết hàn dính với nhau khi nung nóng đủ dưới áp suất. Tác động áp suất được giữ cho đến khi mối hàn nguội đi. Phương pháp này rất thường được sử dụng trong ngành chế tạo khung xe và chế tạo thiết bị. Với phương pháp hàn ép, thợ cơ điện tử ít khi phải đối mặt như là người sử dụng, mà thường dưới danh nghĩa người đứng máy (giám sát) hoặc người bảo trì thiết bị hàn ép, được sử dụng trong các thiết bị sản xuất ô tô.
Phương pháp hàn nóng chảy
Các vật liệu nền được nung nóng tại vị trí hàn tới nhiệt độ nóng chảy. Trạng thái lỏng này dẫn đến sự pha trộn các vật liệu nền. Để điền đầy vào khe hở hàn, thông thường người ta bổ sung thêm vật liệu tương tự (cùng loại) để xử lý vật liệu nóng chảy. Lúc hóa rắn (đông cứng), vật liệu nền và vật liệu bổ sung cấu tạo thành một cấu trúc chung.
Ở hàn nóng chảy, sự hợp nhất xảy ra qua sự pha trộn vật liệu hóa lỏng.
Phương pháp hàn nóng chảy (Hình 2) được phân loại theo cách cung cấp nhiệt. Hai loại quan trọng nhất là hàn nóng chảy bằng khí (hàn gió đá, hàn với oxy acetylen) và hàn hồ quang.Hàn gió đá (hàn hơi, hàn nóng chảy bằng khí)
ở hàn gió đá, chỗ kết nối được nung nóng bằng mỏ hàn (Hình 1). Qua đó, năng lượng nóng chảy cần thiết được tạo ra thông qua việc đốt cháy hỗn hợp khí oxy. ờ đây acetylen được sử dụng chủ yếu làm nhiên liệu. Hàn gió đá đóng vai trò thứ yếu trong lĩnh vực cơ điện tử và hầu như chỉ được sử dụng trong trường hợp không có sẵn năng lượng điện.
Phương pháp hàn nóng chảy với hồ quang (Hình 2)
Trong phương pháp này, nhiệt nóng chảy cần thiết được tạo ra bởi hồ quang điện. Máy phát điện thay đổi cường độ dòng điện và điện thế tương ứng theo yêu cầu. Sự khác biệt ở những phương pháp này chủ yếu là cách thức mà các vùng kim loại nóng chảy được bảo vệ trước khi cung cấp không khí. Thông thường ở hàn hồ quang kim loại, điều này được thực hiện bằng que hàn có vỏ bọc. ở phương pháp hàn khí bảo vệ, các khí bảo vệ khác nhau được sử dụng cho việc này.
Tất cả những phương pháp này có các điểm chung quan trọng, bao gồm máy phát điện hàn, quá trình trong hồ quang và việc phòng ngừa tai nạn.
Máy phát điện hàn
Dòng điện đạt yêu cầu để hàn phải có cường độ cao, điều chỉnh được và điện thế thấp. Điện thế theo các quy định phòng ngừa tai nạn không được vượt quá một số giá trị nhất định. Dòng điện hàn có thể tạo ra từ bộ biến thế, bộ chỉnh lưu hoặc máy phát điện, ở bộ chình lưu hàn, trước tiên điện xoay chiều được đổi từ bộ biến thế của lưới điện rồi chuyển thành điện một chiều thông qua bộ chỉnh lưu.
Máy phát điện hàn (Hình 3) được sử dụng để tạo ra điện một chiều. Máy phát điện thường được dẫn động bởi một động cơ điện, hiếm khi dùng động cơ đốt (động cơ nổ) truyền động và chuyển đổi năng lượng cơ học cúa chuyển động quay thành năng lượng điện.
Sự hình thành hồ quang (Hình 4)
Nhiệt cần thiết làm nóng chảy được tạo ra từ hồ quang. Điều này xảy ra sau khi gõ nhẹ (chấm ngắn), tạo một “ngắn mạch” giữa điện cực và chi tiết như là cực dương và cực âm, để việc di chuyển điện tử được vận hành. Luồng điện tử này (dòng electron) vẫn tiếp tục sau khi nâng que hàn lên tạo ra một khe không khí nhỏ mà qua đó hình thành hồ quang. Điều này tạo ra một sự “va đập” của rất nhiều các điện tử trên bề mặt nung nóng bằng động năng lớn. Năng lượng nhiệt qua đó phát sinh đủ để đạt nhiệt độ nóng chảy trên 4000 °c.Phương pháp hàn hồ quang trong môi trường khí trơ (khí bảo vệ)
ở lĩnh vực này ta phân biệt hàn hồ quang kim loại và hàn hồ quang trong môi trường khí bảo vệ wolfram. Trong phương pháp này, vùng kim loại nóng chảy (vũng hàn) được che chắn ảnh hường bất lợi của không khí. Khí trơ (khí hiếm), khí hoạt hóa hay khí hỗn hợp được sư dụng làm khí bảo vệ. Khí hoạt hóa và khí hỗn hợp có nhiều khuyết điểm hơn so với các loại khí trơ bảo vệ, vì chúng phản ứng với vùng kim loại nóng chảy vả giảm chất lượng cơ học của mối hàn. Khuyết điểm này có thể bù đắp một phần bởi một hợp phần tương ứng của dây hàn bổ sung. Phương pháp hàn hồ quang với khí bảo vệ thay thế gần như hoàn toàn hàn gió đá.
Hàn hồ quang kim loại trong môi trường khí bảo vệ (Hình 1)
Trong phương pháp này hồ quang dòng điện một chiều cháy giữa dây điện cực trơn nóng chảỵ và chi tiết. Dây hàn có đường kính từ 0,8 mm đến 2,4 mm quấn trên một cuộn dây được sử dụng làm cực dương của dây điện cực. Một thiết bị dẫn tiến đẩy dây theo tỷ lệ tốc độ nóng chảy của nó thông qua súng hàn. Dòng điện hàn được dẫn đến dây hàn trong súng hàn ngay trước hồ quang qua công tắc điện di động. Lắp đặt một hệ thống làm nguội bằng không khí hoặc nước sẽ làm giảm sự nung nóng của súng hàn. Phương pháp hàn hồ quang kim loại với khí bảo vệ được phân chia theo việc ứng dụng các loại khí bảo vệ.
Trong MIG (hàn bằng điện cực nóng chảy trong môi trường khí trơ) chủ yếu là argon được sử dụng làm khí bảo vệ. Khí hiếm này là loại đắt tiền, nhưng có thể cho các mối hàn tốt. Đặc biệt là đạt được năng suất hàn cao ở tấm kim loại trung bình và dày. Phương pháp hàn MIG được ứng dụng cho thép không gỉ, kim loại phi sắt và kim loại nhẹ.
ở hàn kim loại trong môi trường khí bảo vệ hoạt tính (MAG), người ta sử dụng khí hoạt tính với giá thành hợp lý hơn (rất thường xuyên là khí co2 hoặc khí hỗn hợp). Ngoài ra phương pháp này tương ứng trong kỹ thuật và ứng dụng với phương pháp hàn MIG. Hàn MAG được áp dụng chủ yếu cho thép hợp kim thấp và không hợp kim, đặc biệt trong ngành thiết kế khung xe để hàn các tấm kim loại mỏng.
Hàn bằng điện cực không nóng chảy wolfram trong khí trơ (Hình 2)ở hàn wolfram trong khí trơ (WIG), hồ quang cháy giữa điện cực wolfram không nóng chảy và chi tiết. Vật liệu bổ sung có thể được cung cấp từ phía bên cạnh. Bằng phương pháp này mối hàn được thực hiện có chất lượng tốt và đều đặn, chủ yếu dùng tốt cho thép hợp kim cao, kim loại phi sắt và kim loại nhẹ.
6.8 Dán (sự kết dính)
Qua phương pháp dán, vật liệu được kết nối với nhau bằng vật liệu không tách (tháo) rời.
Ngày nay phương pháp dán trong kỹ thuật trở nên rất quan trọng và bổ sung vào các phương pháp kết nối thông thường đến nay.
Cách thức tác dụng của kết nối dán
ở kết nối dán, lực cố kết tác động giữa các hạt chất kết dính cũng như lực bám giữạ các hạt chất kết dính và vật liệu. Đối với vật liệu xốp như gỗ, giấy, hàng dệt và các loại khác, chất kết dính thâm nhập vào các lỗ bọng và có thêm sự ăn khớp (đan xen) cơ học (Hình 1). Qua đó kết nối đạt được độ bền cao. Khi kết dính ở bề mặt láng như thép, độ bền kết nối chỉ bị tác động bởi lực cố kết và lực bám. Điều kiện cho sự kết dính là tẩm ướt đều bề mặt kết nối (xem hàn vảy). Các chất kết dính cũng phải được phân phối đều và không được tạo thành hạt. Độ bền nơi dán tùy thuộc vào chất kết dính được sử dụng, kết cấu bề mặt dán, vật liệu chi tiết dán và các loại ứng lực.
Chất kết dính cho kim loại
Ở chất kết dính (keo dán) dung môi, chất kết dính hòa tan trong dung môi. Để dán các chi tiết, dung môi phải bay hơi hoặc các chất kết dính phải được hoàn toàn thông hơi trước khi kết nối. Vì thế với chất kết dính dung môi, đa số kim loại có thể dán được với các vật liệu xốp (gỗ, da, một số loại nhựa).
Chất kết dính phản ứng được sử dụng cho kết nối dán thuần túy kim loại. Trong đó sự biến cứng xảy ra qua quá trình hóa học, với hệ quả là một kết nối cố định (so sánh chất dẻo). Khi biến cứng, các phân tử kết dính đơn thể kết nối thành chuỗi và mạng.Chất kết dính trong đó sự biến cứng xảy ra ở nhiệt độ phòng còn được gọi là keo dán nguội (Hình 3). Thuộc về nhóm này có keo dán hai thành phần, nghĩa là để biến cứng, keo dán được trộn với một thành phần thứ hai, chất làm hóa cứng (Hình 4). Vì sự biến cứng dần dần bắt đầu sau khi trộn, các chất kết dính phải được xử lý ngay lập tức. Thời gian trong đó có thể xử lý chất kết dính được trộn gọi là thời gian xử lý. Thời gian này được nhà sản xuất quy định. Trong một số keo dán nguội thời gian biến cứng có thể giảm qua nung nóng.
Chất kết dính đòi hỏi nhiệt và áp suất trong quá trình biến cứng được gọi là keo dán nóng.
Keo dán nống thuộc về nhóm keo dán một thành phần, trong đó chứa tất cả các thành phần đã trộn. Chúng đạt được độ bền khoảng gấp đôi so với chất kết dính nguội, nhưng đòi hỏi nhiều công sức kỹ thuật để thực hiện sự biến cứng bằng cách nung nóng dưới áp lực (nén).
Các chất kết dính kim loại kỹ thuật được sử dụng trong thực tế thường là chất kết dính phản ứng và bao gồm chủ yếu bốn hệ thống chất kết dính (Bảng 1). Từ tên thương mại ta không biết được rõ ràng thành phần của chất kết dính. Các nhà sản xuất chất kết dính thường cung cấp keo dán kỹ thuật, được tối ưu hóa cho từng mục đích ứng dụng riêng biệt. Để có được tính chất đặc biệt, người ta thường pha trộn nhiều hệ thống kết dính với nhau.Cấu trúc và sàn xuất kết nối dán
Tính chất của keo dán phải được chú ý khi thiết kế cấu trúc kết nổi dán, vì độ bền kéo của nó chỉ bằng khoảng 10% của thép. Bề mặt dán nên tránh chịu tải kéo không đối xứng, lột (tróc) hoặc tách ra (Hình 1 và Hình 2).
Các loại ứng lực (tải) thích hợp cho kết nối dán là xoắn và cắt.
Những bước gia công quan trọng nhất khi gia công kết nối dán là:
■ Chuẩn bị vị trí dán
■ Pha trộn và cân đo chất kết dính
■ Bôi (trét) các chất dán
■ Ép các chi tiết vào nhau
■ Biến cứng lớp keo dán
Để chuẩn bị vị trí dán, các bề mặt phải được tách mỡ (khử mỡ, tẩy dầu) và mài v.v, với yêu cầu cao bằng phun cát, phương pháp làm nhám bề mặt bằng cơ học. Các phương pháp hóa học cũng thích hợp như ăn mòn và điện giải với công đoạn rửa kỹ lưỡng tiếp theo.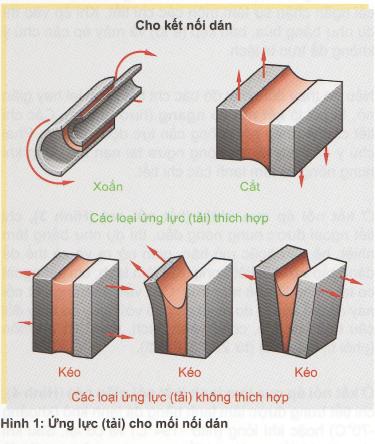
Khi pha trộn và cân đo phải chú ý quy định gia công của nhà sản xuất keo dán. Các chất kết dinh sau khi pha trộn ngay lập tức được phân phối mỏng trên bề mặt dán bằng cọ, bay hay với thiết bị định lượng. Các chi tiết sau khi ép vào nhau phải đảm bảo không bị xê dịch.Trước khi dùng cần giữ đủ thời gian biến cứng.
6.9 Kết nối ép
Phương pháp kết nối này dựa trên sự lắp ghép ép, nghĩa là lắp ghép có độ dôi giữa các bộ phận bên trong và bên ngoài. Trong kết nối này vật liệu bị biến dạng đàn hồi. Nó gây ra lực ma sát cao và có thể truyền momen quay lớn và lực dọc trục kết nối qua ma sát mà không cần thêm phương tiện kết nối.
Khi chế tạo kết nối, tùy thuộc vào nhiệt độ mà ta phân biệt nhiều loại két nối khác nhau (Hình 1):
Kết nối ép dọc (dọc trục) (Hình 2) ở nhiệt độ bình thường đạt được bằng cách ép dọc theo chiều trục vào trong lỗ. Trục phải có cạnh vạt nhỏ (đến 5°) để tránh làm nhẵn thái quá bề mặt vật liệu. Việc tháo rời và ráp lại kết nối được lặp đi lặp lại gâỵ ra hậu quả là lực bám giảm mạnh. Bôi trơn mỏng đầu trục với dầu cải ngăn chặn sự làm mòn các chi tiết. Khi ép vào thí dụ như bằng búa, bàn kẹp (ê tô) và máy ép cần chú ý không để trục bị lệch.
Nếu do thay đổi nhiệt độ các chi tiết bị co lại hay giãn nở, ta gọi là kết nối ép ngang (hướng tâm). Các chi tiết có thể ghép nối không cần lực dọc trục lớn. Phải chú ý đến quy định phòng ngừa tai nạn lao động khi nung nóng và làm lạnh các chi tiết.
Ở kết nối ép qua nhiệt (kết nối cơ) (Hình 3), chi tiết ngoài được nung nóng đều, thí dụ như bằng tấm nhiệt, bể dầu hoặc mỏ hàn, giãn nở ra và có thể dễ dàng ráp vào chi tiết trong. Khi làm lạnh, chi tiết ngoài co lại và ép lên bề mặt trục. Các vấn đề trong kết nối này có thể xảy ra do nhiệt độ cao với nguy cơ thay đổi cấu trúc tinh thể, cong vênh (lệch, méo) và ăn mòn (phôi bị oxy hóa) (từ 250°C trở đi).
Ở kết nối ép qua làm lạnh (kết nối giãn nở) (Hình 4), chi tiết trong được làm lạnh bằng đá lạnh khô (khoảng -70°C) hoặc khí lỏng (nitơ -194°C) và co lại. Sau khi ráp với chi tiết ngoài, chi tiết trong nóng trở lại nhiệt độ thường và nở ra. Khớp nối ép qua làm lạnh có nhiều lợi thế, thí dụ không xảy ra sự thay đổi cấu trúc tinh thể khi xử lý nhiệt (trui, tôi) các bộ phận, tuy nhiên chi phí cho chất làm lạnh tương đối cao và chênh lệch nhiệt độ đạt được thấp.
Trong trường hợp đặc biệt người ta có thể kết hợp hai phương pháp với nhau. Như vậy chi tiết ngoài được làm nóng và chi tiết trong được làm lạnh.
Tính toán nhiệt độ kết nối
Một bánh răng được ráp với trục có đường kính Ф 30 H7/ s6 bằng khớp nối ép qua làm lạnh. Độ hở khi lắp ráp là
10 micron (μ). Trục phải được làm lạnh đến nhiệt độ nào? Nhiệt độ bình thường 20°C.
Trục phải được làm lạnh tới -141 °C. Nhiệt độ âm này chỉ đạt được với không khí lỏng (nitơ -194 °C) hoặc oxy lỏng (-183°C).
6.10 Kết nối kẹp chặt và uốn nếp (gấp nếp)
Ngoài các kỹ thuật kết nối cổ điển được mô tả, trong những năm gần đây một loạt kết nối được phát triển và phổ biến đặc biệt là trong lĩnh vực kỹ thuật điện.
Vì vậy, thí dụ các chi tiết rời của các ống dẫn cáp không còn bắt vít theo quy tắc trong việc cất giữ các dây dẫn điện, mà móc tại vị trí được định trước (Hình 1). Loại kết nối này được gọi là kết nối cắm tác động nhanh và thuộc nhóm kết nối tháo rời được.
Cũng như vậy, các loại kết nối kẹp chặt khác nhau có thể tháo ra được (Hình 2) phần nhiều hoạt động trên cơ sở kết nối vít.
Ngược lại, các lực giữ được tạo ra tại kết nối kẹp lò xo qua tác động lò xo của một móc kim loại uốn cong (Hình 3). Loại kết nối này thường được sử dụng để nối dây đồng nhỏ. Để nối dây dẫn điện, thí dụ ở một thanh dẫn, lò xo lồng được ấn xuống và đưa dây đồng cách điện vào lỗ hổng. Kết nối lò xo lồng kéo rát dễ tháo rời, hơn nữa gần như không cần bảo trì và đặc biệt là chống rung.Kết nối cắm trên bo mạch điện tử cũng tuân theo đúng quy luật của kỹ thuật ghép nối. Chúng bao gồm một ổ cắm dạng dao và một ổ cắm lò xo. ổ cắm gắn lên bảng mạch in và bộ nối vào khung thiết bị. Thí dụ ứng dụng điển hình là thẻ đồ họa hoặc thẻ chèn khác được sử dụng trong máy tính.
Một kết nối an toàn của dây đồng trong vị trí kết nối thích hợp, thí dụ qua đuôi cắm dây (ống bọc đầu cuối cho dây điện). Những dây được gắn vào đuôi và tạo nếp kết nối chặt bằng một dụng cụ phù hợp (chuyên dùng) (Hình 4 và 5). Trong thực tế kỹ thuật này được xếp loại là không tháo được, cũng được gọi là ép hoặc Crimpen (tiếng Anh).Bài tập:
1. Hàn vảy mềm khác hàn vảy cứng như thế nào?
2. Hàn vảy và hàn khác nhau như thế nào về mặt vật lý?
3. Mô tả các quá trình khi hàn vảy và hàn.
4. Quy tắc làm việc nào cần được lưu ý khi hàn vảy?
Bài tập:
Một bàn được chế tạo bằng protin nhôm cho thiết bị xử lý thao tác bằng điện-khí nén được miêu tả theo (Hình 1). Các kích thước của tấm đế là 300 mm X 600 mm. ở mặt dưới được chia thành lưới với ô vuông 50 mm và rãnh 8 mm.
1. Hãy vẽ tay một bản phác họa cho khung. Qua đó hãy khảo sát nhiều lựa chọn thiết kế và quyết định một giải pháp. Giải thích sự lựa chọn của bạn.
2. Hãy chọn một protin phù hợp từ danh mục protin của nhà cung cấp. Nếu cần, có thể sử dụng các thông tin trên mạng của nhà sản xuất.
3. Hãy tìm các bộ phận kết nối cần thiết. Lưu ý bàn cần có độ ổn định đủ cao chống lại lực tác động ngang.
4. Hãy tạo một bản vẽ lắp ráp và bản vẽ chi tiết cần thiết.
5. Nhiều nhà sản xuất cung cấp chương trình CAD hỗ trợ tạo ra bản vẽ, dễ dàng thao tác có sẵn trên mạng Internet hoặc trên CD-ROM. Hãy sử dụng các chương trình này nếu có cơ hội.
6. Tổng hợp lại những chi tiết cần thiết với nhau trong một danh mục chi tiết. Chú ý đến cách đặt tên theo chuẩn của các bộ phận tiêu chuẩn.
7. Hãy xác định các phương pháp gia công cần thiết cho việc chế tạo.
8. Dụng cụ nào cần thiết?
9. Hãy tạo một kế hoạch làm việc điển hình cho hai chi tiết để sản xuất. Xác định các việc làm tương ứng và những dụng cụ cần thiết.
10. Hãy tạo một kế hoạch làm việc thứ tự để lắp ráp các chi tiết rời.
Nhất nghệ tinh cơ điện tử |