Ước muốn có thể chuyển các công việc nặng nhọc và khó khăn sang máy móc và tự động hóa đã có từ rất lâu. Ngược dòng thời gian, những hệ điều khiển bằng cơ học đã xuất hiện từ thế kỷ 18 (thí dụ như khung cửi dệt cơ khí). Vào năm 1770 p. Jaquet-Droz đã chế tạo búp bê viết chữ trên giấy bằng ngòi bút (Hình 1). Đây là những hệ điều khiển thuần cơ khí bằng các đĩa điều khiển được thay thế, thậm chí chúng có thể viết những hàng chữ khác nhau.
Ngay từ giữa thế kỷ 20, người ta đã tìm kiếm máy công cụ được điều khiển bằng số. Tất cả các thông tin dữ liệu về gia công xuất hiện dưới dạng những trị số; thí dụ vận tốc dẫn tiến, vận tốc cắt, kích thước hình học của chi tiết. Ngay cả việc mô tả quỹ đạo bằng toán học theo lý thuyết cũng thường có khả năng thực hiện được (thí dụ như quỹ đạo phức tạp của máy bay), tuy nhiên vào lúc đó việc chế tạo với sự trợ giúp của dưỡng chép hình lại quá thiếu chính
Sau thế chiến thứ hai, những máy công cụ NC đầu tiên được chế tạo tại Mỹ (NC: Numerical Control = Điều khiển kỹ thuật số). Những máy công cụ này sản xuất bằng cách nhận thông số về vị trí (thông số định vị) qua băng đục lỗ. Chúng đã có khả năng tính toán được những trị số chuyển tiếp cho các vị trí này và với động cơ servo điều khiển cũng như điều chỉnh chuyển động của các trục sao cho có thể gia công được cả những biên dạng phức tạp. Thời đó không có bộ nhớ cho chương trình; môi trường lưu trữ thông tin lúc ấy là thẻ đục lỗ và hệ điều khiển không phải là thành phần của máy (Hình 2).
Với sự trợ giúp của bộ vi xử lý, máy NC đã phát triển thành hệ thống điều khiển CNC với lĩnh vực hoạt động rộng lớn (Computer Numerical Control = điều khiển bằng kỹ thuật số với trợ giúp của máy tính, Hình 2 và 3). Ngày nay không còn máy NC dạng cổ điển nữa, vì thế người ta có thể xem khái niệm NC và CNC đồng nghĩa với nhau.
1) TTDLVH (BDE: Betriebsdateneríassung = Thu thập dữ liệu vận hành)
2) TTDLM (MDE: Maschinendateneríassung = Thu thập dữ liệu máy)Việc nối mạng với các máy công cụ cũng được gia táng. Trước đây, người ta hy vọng sẽ tiết kiệm được nhiều hơn bằng cách tập trung tính toán vào việc nội suy quỹ đạo của chuyển động cắt dàn trải từ nhiều máy NC vào một máy chủ hay máy trung tâm với phương pháp gọi là DNC1). Qua đó từng máy NC chỉ còn trang bị với một hệ thống điều khiển không đầy đủ chức năng gọi là hệ thống điều khiển khung vỏ (hệ thống điều khiển thân máy).
Điều này xem ra có vẻ hợp lý vào thời điểm đó vì hệ điều khiển cần thiết cho việc tính toán nội suy có chi phí rất cao. Vì những máy NC đời trước không có bộ nhớ riêng cho chương trình, do đó chúng phải nhận từng câu lệnh một từ máy tính DNC. Tại đây xuất hiện vấn đề với việc cung cấp dữ liệu. Mặt khác việc hạ giá nhanh chóng trong lĩnh vực máy tính đồng thời với khả năng phần cứng được tăng mạnh đã khiến cho phương pháp này hoàn toàn bị phá sản.
Ngày nay người ta hiểu DNC là điều khiển kỹ thuật số phân bố (Distributed Numerical Control). Điều này có nghĩa là nhiều máy tính cũng như công cụ được phân bố qua một mạng LAN (Local Area Network = Mạng cục bộ) (Hình 1).Những chức năng điển hình của một hệ thống DNC như thế gồm:
■ Quản lý, lưu trữ và phân bố những chương trình, dữ liệu của dụng cụ, trị số chỉnh sửa; tự động hóa một phần hay thậm chí toàn bộ. Ngày nay việc quản lý 10.000 chương trình khác nhau không còn là điều hiếm có nữa.
■ Giám sát quy trình gia công và lưu lại nhật ký máy để có thể nhận biết sự bất thường khi vận hành.
■ Trong trường hợp chương trình quá dài, cung cấp tuần tự cho từng máy CNC với những phần chương trình tương ứng để bảo đảm việc xử lý được liên tục.
■ Chuyển trở lại những chương trình và dữ liệu (thông số) chỉnh sửa cho việc quản lý trung tâm để tối ưu hóa quy trình gia công.
■ Điều khiển dòng vật liệu.
■ Thu thập dữ liệu máy (TTDLM) (Hình 2). Dữ liệu máy là thông số riêng của máy (thi dụ như thời hạn bảo dưỡng, tuổi thọ, độ chính xác gia công).
■ Thu thập dữ liệu vận hành (TTDLVH). Dữ liệu vận hành là thông số xuất hiện trong quy trình sản xuất, chúng mô tả diễn biến quy trình (thí dụ như thời hạn giao hàng, số lượng sản xuất, thời gian làm việc).
DNC: Direct Numerical Control = Điều khiển kỹ thuật số trực tiếp
8.1 Đặc tính của máy CNC
Những đặc tính sau đây là điển hình cho máy CNC ngày nay:
■ Việc gia công chi tiết được thực hiện với sự trợ giúp của một chương trình lưu trữ trong một bộ nhớ và được gọi ra vào lúc thực hiện gia công. Trong chương trình này có sẵn những thông tin cần thiết dưới dạng câu lệnh cho gia công như: kích thước hình học của chi tiết, bước dẫn tiến, tốc độ cắt, đỏng/mở dung dịch làm nguội, dụng cụ và thay đổi dụng cụ. Việc nhập liệu cho chương trình được thực hiện qua một vùng điều khiển máy (Hình 1), một máy tính để ngoài (PC công nghiệp), đĩa mềm hay một mạng cục bộ (LAN).
■ Tất cả những đơn vị chuyển động (thí dụ như cốt trục, trục chính, hệ thống thay đổi dụng cụ) có hệ dẫn động riêng (dẫn động độc lập) (Hình 4).
■ Ngay cả trục chính cũng có một động cơ dẫn động có thể điều khiển tốc độ vô cấp (Hình 4) sao cho những kích thước hình học thay đổi như trong khi tiện mặt đầu, tốc độ cắt được giữ cố định qua việc thay đổi số vòng quay tương ứng của trục chính.
■ Mỗi một trục chuyển động hay trục định vị đều có một hệ thống điều chỉnh vị trí và điều chỉnh vận tốc riêng (Hình 4).
■ Qua việc sử dụng trục vít bi quay vòng (Hình 3) trong các trục dẫn tiến, người ta có thể gia công phay nghịch chiều và thuận chiều. Độ rơ (độ hở chuyển động đảo chiều) xuất hiện trong trục ren hình thang sẽ biến mất hầu như hoàn toàn.
■ Việc thay đổi dụng cụ điều khiển bằng chương trình có thể thực hiện được qua hệ thay đổi dụng cụ tự động (Hình 2). Qua đó từng máy riêng rẽ có thể chạy lâu hơn mà không cần người điều khiển máy tác động vào cũng như một người đứng máy có thể điều khiển nhiều máy. Dụng cụ bị mòn hay bị mẻ cố thể thay thế bằng dụng cụ mới.
8.2 Hệ thống đo hành trình
Máy CNC cần một hệ thống đo hành trình cho mỗi cốt trục được điều chỉnh. Hệ thống đo này cung cấp tín hiệu đo điện tử có thể phân tích và đánh giá được. Việc chọn lựa hệ thống đo phù hợp được thực hiện theo nhiều tiêu chí: đoạn đường di chuyển tối đa, tốc độ di chuyển tối đa của cốt trục (láp), độ chính xác, khả năng lắp ráp đơn giản và chi phí. Hệ thống đo hành trình vận hành với nhiều phương pháp khác nhau (Hình 1).
Trong phương pháp đo trực tiếp, việc thu nhận trị số đo được thực hiện trực tiếp ở bàn trượt máy, trong khi ở phương pháp đo gián tiếp thì tại trục dẫn tiến (Hình 2).
Trong phương pháp đo analog, mỗi một vị trí đều có tương ứng một trị số nhất định của một đại lượng vật lý (thí dụ như độ lệch pha của hai điện áp). Trong phương pháp đo digital phạm vi đo được chia nhỏ thành những bước xác định và đếm được.
Hệ thống đo hành trình theo gia số đo với lượng cố định tăng dần từng bước (gia lượng hay gia số) tính từ tình trạng trước đó (Hình 3). ở hệ thống đo tuyệt đối, trị số định vị có sân ngay khi mờ máy để sử dụng.
Ở hệ thống đo hành trình theo gia số, điểm tham chiếu phải tiếp cận trước tiên sau khi mở máy.
Phương pháp đo tuyệt đối cần thiết ở nơi mà vấn đề xuất hiện sau khi việc vận hành bị ngắt quãng vì máy phải được tham chiếu (quy chiếu) mới. Như vậy sẽ mất rất nhiều thời gian khi một robot hàn ở trong thân xe phải tìm lại được điểm tham chiếu bằng tay (thủ công) sau khi bị gián đoạn vì việc chạy tìm điểm tham chiếu một cách tự động sẽ dẫn đến va chạm.
Giữa phương pháp đo tuyệt đối và tương đối (đo theo gia số) là hệ thống đo hành trình giả tuyệt đối (Hình 4). Hệ thống đo có những dấu tham chiếu với các khoảng cách khác nhau được định trước. Như thế vị trí có thể xác định được sau khi chạy qua hai dấu tham chiếu nằm cạnh nhau và hệ thống đo hành trình không cần phải chạy đến điểm tham chiếu gốc. Như vậy chỉ cần chạy qua 2 dấu tham chiếu nằm cạnh nhau là đủ cho hệ thống đo lại nằm ở vị trí được xác định.Việc lập trình của máy CNC hoàn toàn độc lập với hệ đo hành trình được sử dụng. Hệ điều khiển tính toán và chuyển đổi tất cả thông tin dựa vào hệ tọa độ riêng của từng máy.
8.3 Thông tin vị trí và hệ tọa độ
Nếu vị trí của một vật thể rắn (thí dụ như dao phay, dao tiện, kìm hàn của một robot) phải mô tả chính xác trong không gian, người ta cần có toàn bộ sáu thông tin về tọa độ độc lập với nhau. Một mặt đó là thông số về vị trí (thí dụ như X, y và z). Mặt khác người ta còn cần thêm các thông tin về hướng (thí dụ như chuyển động quay A, B và c xung quanh các trục X, y và z (Hình 1). Như thế thông tin về vị trí chính xác của một vật thể rắn trong không gian gồm ba thông số vị trí và ba thông số định hướng. Tùy theo những chuyển động của máy CNC trong không gian phức tạp như thế nào, người ta cần một số lượng trục khác biệt và độc lập với nhau. Vì vậy trong điều khiển 2D (2 chiều), người ta chỉ có thể thay đổi vị trí trong một mặt phẳng trong khi ở hệ thống 3D (3 chiều) việc điều khiển cho phép thay đổi vị trí trong không gian. Từ điều khiển 4D trở đi, ngoài vị trí trong không gian, còn có thêm sự thay đổi về định hướng.
Người ta sử dụng hệ tọa độ Descartes cho nhiều máy CNC để mô tả vị trí; cho các thông tin về hướng còn cần thêm ba chuyền động quay xung quanh các trục đó (Hình 2).
Để đơn giản hóa vấn đề, những điều trình bày sau đây giới hạn vào việc điều khiển 3D. Mỗi một trục trong ba trục có hệ thống đo hành trình riêng biệt. Phần lớn các hệ thống đo hành trình cắt nhau ở điểm gốc máy (điểm 0) M (Hình 3). Điểm gốc này được nhà sán xuất quy định và người sử dụng máy không thể thay đổi. Trong máy tiện, điểm này phần lớn nằm trên cốt trục chính trong mạt chặn củă mâm cặp (Hình 3). ở máy phay thì vị trí của nó phụ thuộc vào quy định của nhà sản xuất.
Nếu không có dụng cụ hoạt động trong quá trình điều khiển thi toàn bộ các thông tin về vị trí dựa vào điểm chuẩn giá mang dụng cụ T (Hình 3).
Khi nhà sản xuất sử dụng hệ đo hành trình theo gia số cho cốt trục máy và nếu không thể tới gần (tiếp cận) điểm gốc máy được (thí dụ như máy tiện vói điểm gốc trong mâm cặp), nhà sản xuất định nghĩa một điểm mới trong phạm vi di chuyển của máy gọi là điểm tham chiếu (điềm chuẩn, điểm quy chiếu) R (Hình 3). Từ điểm này, những khoảng cách theo hướng trục X, y và z đến điểm gốc được xác định. Sau khi mở máy, một quy trình được lập trình trước của nhà sản xuất điều khiển máy đến điểm tham chiếu. Do khoảng cách theo hướng X, y và z đến điểm gốc máy đã được biết chính xác, vì vậy hệ điều khiển được thông báo về vị trí trong không gian.
Khi lập trình phải giả sử rằng tất cả các chuyển động dẫn tiến xuất phát từ dụng cụ đi ra.
8.4 Đo đạc dụng cụ và chỉnh sửa dụng cụ
Sau khi mở máy CNC và khởi động việc quy chiếu cần thiết của từng trục riêng rẽ ở hệ đo hành trình theo gia số (xem trang 238), điểm chuẩn T của giá đỡ mang dụng cụ được đặt trùng vào điểm có trị số của hệ tọa độ đã được lập trình trước.
Nếu dụng cụ được kẹp chặt vào trục quay, hệ điều khiển phải chỉnh sửa lại tất cả lệnh di chuyển của các lưỡi cắt dụng cụ trong gia công cắt gọt. Như thế biên dạng định trước của chi tiết được lập trình không bị lệ thuộc vào dụng cụ được đưa vào sử dụng.
Để làm việc này, cần thiết phải tìm ra trị số chỉnh sửa dụng cụ (thí dụ như chiều dài và đường kính dao phay trong gia công phay). Những trị số này được lưu trữ trong bộ nhớ dữ liệu về dụng cụ. Hệ điều khiển CNC có thề truy cập vào đây để lấy ra và tính toán những chỉnh sửa cần thiết khi vận hành chương trình. Cả khi thay đổi dụng cụ bổ sung thì chỉ phải thay đổi trị số chỉnh sửa chứ không phải chương trình.
Ở cách đo dụng cụ ngoài, việc đo đạc được thực hiện bên ngoài. Để thực hiện mục đích này, dụng cụ được kẹp vào trong một thiết bị chỉnh trước dụng cụ (Hình 1) và đo.
Trong phương pháp đo dụng cụ trong (Hình 2), máy CNC được trang bị với một thiết bị đo bằng phương pháp quang học hay một hộp đo (lực kế) có thể thực hiện việc đo đạc dụng cụ bên trong máy.Cả hai loại đo dụng cụ nói trên đều có một điểm chung là qua đây các trị số chỉnh sửa dụng cụ được tìm ra và chuyển tiếp đến hệ điều khiển bộ lưu trữ dụng cụ. Người ta xác định được khoảng cách của điểm chuẩn cạnh cắt p đến điểm chuẩn dụng cụ E (trị số hiệu chỉnh theo truc X của đầu mũi dao so với điểm chuẩn của giá đỡ dụng cụ, trị số chỉnh sửa chiều dài z) (Hình 3). ở đây cần lưu ý đến dấu của trị số chỉnh sửa. Sự sai dấu có thể dẫn đến máy bị phá hỏng. Việc quy định dấu để tìm ra trị số chỉnh sửa lại tùy vào hệ điều khiển của từng máy. ở Hình 4 theo lý thuyết, hệ tọa độ cần phải dịch chuyển đến điểm p để tìm ra trị số chỉnh sửa. Ta có trị số chỉnh sửa X + 85 mm và z + 41 mm.
Nếu dao cắt nằm tại giá giữ dụng cụ của máy CNC, điểm chuẩn dụng cụ nằm trùng vào điểm chuẩn giá giữ dụng cụ T (Hình 4).
8.5 Loại điều khiển
Tất cả các loại máy điều khiển kỹ thuật số có điểm chung là cùng dựa vào một hệ tọa độ để định nghĩa những điểm và cũng có thể cả phương hướng trong không gian. Việc định nghĩa này được thực hiện hoặc qua cách thông báo trực tiếp tọa độ chính xác (thí dụ trong tiện hay phay) hoặc qua cách dạy làm mẫu (thuật ngữ tiếng Anh gọi là tech = dạy), có nghĩa là thu thập tọa độ bằng cách dẫn robot thực hiện chuyển động khi gia công. Qua việc nhập dữ liệu vào, chính ngay trong chương trình những lệnh tương ứng được xác định, thí dụ như sẽ đi bằng đường nào (chẳng hạn như đường thẳng, vòng tròn) giữa các điểm.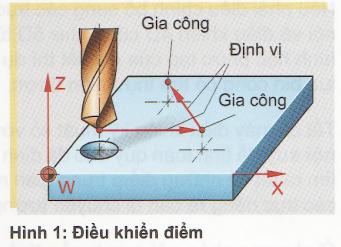
Khả năng thứ ba là xác định dạng quỹ đạo và vận tốc của nó qua một phương pháp gọi là Play-Back hay lập trình nhại lại (lập trình qua cách lặp lại quá trình gia công đã được thực hiện bằng tay trước đỏ). Phương pháp này được sử dụng rất nhiều trong robot phun sơn. Người thao tác (người vận hành máy) dẫn robot chạy bằng tay và hệ điều khiển lưu trữ tất cả dữ liệu, thí dụ như tọa độ các vị trí và vận tốc di chuyển.
8.5.1 Điều khiển điểm
Ở tính năng điều khiển điểm (Hình 1), chuyển động – phần lớn là chuyển động nhanh – được thực hiện từ điểm bắt đầu đến điểm đích. Quãng đường giữa điểm đầu và điểm cuối không thể thấy trước một cách chính xác.
Người ta phân biệt hai loại tính năng điều khiển điểm. Trong tính năng điều khiển điểm không đồng bộ, các trục cần di chuyển được chuyển động đồng thời với vận tốc tối đa. Nếu quãng đường di chuyển của từng cốt trục riêng lẻ không dài bằng nhau, thời gian di chuyển của từng cốt trục cũng khác nhau (ở cùng vận tốc tối đa cho tất cả các cốt trục) và như thế phần lớn các trục không đạt điểm đích cùng một lúc.
ở tính năng điều khiển điểm đồng bộ, các trục đạt đến điểm cuối đồng thời dù các đoạn đường di chuyển dài ngắn khác nhau. Điều này được thực hiện qua việc thích ứng (làm cho phù hợp) các vận tốc chuyển động riêng của từng trục. Trục có thời gian di chuyển dài nhất sẽ được xem là trục làm chuẩn. Các trục khác sẽ giảm vận tốc sao cho tất cả các trục cùng chuyển động với thời gian như nhau. Các loại robot đơn giản, máy khoan NC, máy đột dập hay hàn điểm được trang bị với hệ điều khiển điểm thuần túy.
8.5.2 Điều khiển theo quỹ đạo (điều khiển biên dạng, điều khiển theo contua)
Ở điều khiển theo quỹ đạo, các chuyển động phối hợp được thực hiện trong cùng một thời gian ờ hai hay nhiều trục.
Nếu các quỹ đạo cần điều khiển chỉ nằm trong một mặt phẳng, người ta nói về hệ điều khiển 2D (2 chiều), ờ đây hai trục có thể chuyển động đồng thời phối hợp với nhau. Có loại điều khiển tùy chỉ có thể tính nội suy trong một mặt phẳng nhưng lại có thể thực hiện nội suy trong nhiều tầng (mặt phẳng) khác nhau. Loại điều khiển này được gọi là điều khiển 2 1/2D. ở đây chỉ có hai trong ba mặt phẳng được điều khiển phối hợp đồng thời. Việc lựa chọn mặt phẳng để gia công (Hình 2 và 3) do người vận hành máy quyết định.
Với một hệ điều khiển 3D (3 chiều) người ta có thể thực hiện chuyển động trong không gian, ở đây ba trục có thể chuyển động phối hợp với nhau đồng thời (Hình 2).Nếu phải điều chỉnh bổ sung các trục quay vào ba trục chuyển động thẳng để định hướng dụng cụ, người ta sẽ nói vê điều khiển 4D cũng như 5D tùy theo số trục điều khiển (Hình 1). Qua đây việc gia công các kích thước hình học phức tạp của chi tiết thí dụ như các khuôn đúc áp lực (khuôn đúc phun, xịt, tiêm), khuôn rèn và cánh tua bin cong có thể thực hiện được.
Tất cả máy điều khiển kỹ thuật số với hệ điều khiển theo quỹ đạo (theo biên dạng) có điểm chung là cần một bộ nội suy để tính toán quỹ đạo đã định trước này cho chuyển động giữa hai điểm trong không gian. Bộ nội suy này tìm ra tất cả những điểm trung gian nằm trên quãng đường đi đã được định nghĩa bằng toán học và dẫn hướng các trục riêng rẽ cần di chuyển tương ứng với đường cong của quỹ đạo trong không gian.
ờ phương pháp nội suy tuyến tính (nội suy đường thẳng), quỹ đạo là một đường thẳng giữa điểm khởi đầu và điểm cuối. Bộ nội suy không cần các thông tin khác để tính các điểm trung gian; thí dụ như trong công đoạn tiện hoặc phay: G01, ở robot: LINEAR.
Trong phép nội suy đường tròn, chuyển động nằm trên một vòng tròn hay một phần vòng tròn. Bên cạnh điểm đầu và điểm cuối còn cần thiết phải thêm vào chiều quay (theo chiều kim đồng hồ hay ngược lại) và một điểm phụ trên vòng tròn hay tâm điểm mà chuyển động sẽ chạy quanh, thí dụ như trong tiện/phay: G02/ G03; trong robot: CIRCULAR. Sự tính toán trở nên phức tạp nếu trong việc tính quỹ đạo phải bao gồm phần định hướng của dụng cụ phay (trong điều khiển 4D và 5D). Hình 2 mô tả các loại điều khiển khác nhau với những thí dụ trên mặt phẳng.
Đường biểu diễn 1: Điều khiển biên dạng, nội suy tuyến tính:
Chuyển động trên một đường thẳng;
Vì Sx > Sy và cả hai trục cần phải đến điểm đích cùng một lúc, nên vx và Vy không bằng nhau (vx > Vy). Nếu bỏ qua không xét đến giai đoạn tăng tốc, ta có vx = không đổi và Vy = không đổi.
Đường biểu diễn 2: Điều khiển biên dạng, nội suy đường tròn:
Chuyển động trên một cung tròn chung quanh tâm điểm M2;
Vì hai trục cần đến điểm cuối cùng một lúc nên ở đây vx và Vy cũng không bằng nhau, thêm vào đó vx và Vy thay đoi (không cố định). Như ta thấy ở Vy, thậm chí vectơ vận tốc còn đổi chiều.
Đường biểu diễn 3: Điều khiển điểm (đồng bộ);
Chuyển động 2 trục quay;
Hai trục quay phải đi qua những đoạn đường khác biệt. Chúng chạy với vận tốc khác nhau nhưng không đổi (không kể đến giai đoạn tăng tốc cũng như hãm lại) và đến đích đồng thời.
Đường biếu diễn 4: Điều khiển điểm (không đồng bộ); Chuyển động hai trục di chuyển theo đường thẳng (tuyến tính);
Lúc đầu cả hai trục dịch chuyền đồng thời với cùng vận tốc (Độ dốc của đường thẳng là 45°), rồi chỉ còn một chuyển động của trục X đến khi đạt điểm đích; như thế hai trục đến điểm cuối không cùng một thời điểm.Bài tập:
1. Cho biết cặn kẽ ưu và nhược điểm của phương pháp đo trực tiếp và gián tiếp.
2. Trình bày chi tiết ưu và nhược điểm của cách đo tuyệt đối và đo theo gia số.
3. Trình bày chi tiết sự khác biệt giữa máy phay haỵ máy tiện loại thường và loại máy CNC theo số lượng động cơ và số lượng hộp số truyền động (dẫn động).
4. Giải thích khái niệm điều khiển điểm, điều khiển đoạn thẳng và điều khiển quỹ đạo (đặc biệt ở đây: hệ điều khiển 2D, 2 1/2 D, 3D, 4D và 5D).
5. Trình bày lý do mỗi một hệ điều khiển trong câu hỏi 4 cần bao nhiêu động cơ dẫn động.
6. Hãy giải thích khái niệm bộ nội suy. Hãy cho biết ba loại nội suy. Diễn giải vấn đề qua thí dụ một đường thẳng.
7. Người ta cần bộ nội suy cho loại điều khiển nào được nêu lên ở câu 4 (Nêu lý do).
8. Loại điều khiển nào cần thiết tối thiểu cho việc tiện một quả cầu.
9. Hãy diễn giải tính năng vận tốc của trục cần được điều khiển trong câu 8.
10. Hãy xác định tọa độ điểm gốc của chi tiết gia công trong tọa độ máy (Hình 1 và 2).
11. Hãy xác định tọa độ của tâm điểm dụng cụ phay trong tọa độ máy khi lệnh điều khiển là: Chạy đến X30, Y,Z-10 (Hình 2).
12. Hãy tìm trị số chỉnh sửa dụng cụ (Hình 3) cho cả hai dụng cụ theo Hình 4, trang 240.
13. Sự trao đổi dấu có tác động như thế nào trong việc chỉnh sửa dụng cụ?
a) Hãy phác họa một bản vẽ.
b) Tìm tọa độ trong tọa độ máy với sự trợ giúp của Hình 3 và Hình 1.
14. Phác họa các chi tiết phải được phay với hệ điều khiển 3D, 4D và 5D.
15. Vì sao và khi nào máy CNC cần thiết phải có điểm chuẩn (điểm tham chiếu)?
16. Hãy giải thích khái niệm bộ giải góc (Resolver= thiết bị báo vận tốc và vị trí góc).
17. Loại động cơ dẫn động nào được sử dụng trong truyền động (qua) trục và truyền động dân tiến. Hãy chỉ dẫn qua bảng vẽ ưu và nhược điểm của những kiểu động cơ khác nhau.
18. Hãy tìm ở các nhà sản xuất trên internet chiều dài tối đa có thể đạt được trong những hệ đo hành trình tuyệt đối theo đường thẳng và bề rộng của từng rãnh đơn (từng rãnh riêng lẻ, từng rãnh một) là bao nhiêu.
Nhất nghệ tinh cơ điện tử